Data Loading...
Cornejo & Sons December 2018
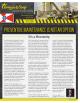
36 Downloads
10.47 MB
Twitter Facebook LinkedIn Copy link
RECOMMEND FLIP-BOOKS
a Summit Materials company
www.cornejocorp.com 316-522-5100
DEC 2018
PREVENTIVE MAINTENANCE IS NOT AN OPTION It’s a Necessity
so many. You can use infrared thermographic cameras for inspections. In the past, I’ve used vibration analysis, electric motor current analysis, and other tools to identify issues before a unit fails. We’ve also implemented electronic inspections using an app. It gives detailed lists of things to look at for a particular piece of equipment. It also acts as a GPS device, not only coaching the operator on what to look for, but also functioning as a communications tool. If the operator is out there doing a section, they can note that something is deficient, select it on the app, and submit it for inspection. It goes through the job cycle, and we confirm that there’s an issue. That starts the scheduling process —we shoot an email to our SUP so they can start scheduling. The inspection app is proving to be a huge benefit. Making sure proper inspections are done continues to be my biggest focus. At Cornejo & Sons, safety is always our top priority, and inspections are a crucial part of maintaining that safety. If we can react to something when it’s just starting to showwear or just starting to generate heat, the repair will be smaller. If you wait until something blows, scheduling will be more difficult, and the repair will need to be made right then and there — in the middle of a landfill or during a bridge deck pour. If we can identify a problem early and
Often, the people you’re trying to influence are used to doing things a certain way. You have to change attitudes and sell them on why proper inspections are so important. The first step is to indicate the compelling reason for the change: better uptime, lower costs, and increased efficiency. I’ve always noticed that once uptime increases, morale improves because crews aren’t just waiting for something to break; they can rely on their equipment. It means we get to the next job faster, and sometimes it means bonuses for the Company if we finish a job early. At companies I worked for in the past, I would go to a job site and ask the crew about an equipment failure. “Something just happened, Jeff,” was the answer I almost always got. I don’t accept that. That’s only part of the reason something fails. Generally, something gives you a sign before it fails — you just have to look for it. Maybe you didn’t have the tools to see that sign, or maybe you didn’t know something was off. If a piece of equipment has always been incorrectly calibrated or set up from the beginning and you’ve looked at it every day, it becomes “right,” to you, and when it eventually fails, “something just happened.” It becomes a training issue, and it’s my responsibility to make sure we develop systems so that everyone knows what’s right and what’s wrong when it comes to equipment.
As the Area Assets Manager at Cornejo & Sons, I’m working to keep all of our assets, including equipment, in working order. I manage equipment and assets from beginning three-year forecasting to current- year forecasts. From specifying and acquiring to managing equipment, I see it through its full lifecycle and determine when it needs a replacement. When I started, I worked with our teams to implement more formal processes for maintenance and sat on many of the Summit Materials steering committees so that those processes could be implemented company- wide. I want to get every team member on board with the importance of inspections because I’ve noticed how effective they are. That’s led us to implement preventive maintenance scheduling for systems and processes; for example, we schedule all of our mobile equipment at regular intervals, every 250 or 500 hours. All operators are required to do pre-shift inspections for all equipment. Each inspection form is specific to the equipment type and instructs the operators on how to perform the inspection. Of course, I knowwhy inspections are important, but it’s another thing to demonstrate that to my team. Effective change is a challenge. You have to illustrate it by informing them, “Did you all realize we lose 20 percent of our scheduled hours due to equipment being down?” That’s the challenge — your reason for wanting change has to be valid.
schedule the repair when crews aren’t working, it’s better for everyone. Jeff Bremer
You have to have the right tools to allowyou to see a problem, and technology has given us
316-522-5100 1
CHIP AND DAN HEATH’S ‘MADE TO STICK’
We believe that small businesses can have a positive impact on local communities and the wider world. A successful charity campaign can make a world of difference for people in need, especially over the holidays. But not all charitable organizations are created equal, and supporting the wrong organization can do more harm than good. Here are some tips on finding the best fit for your business. ALIGN MISSIONS When narrowing down the thousands of local and national charities you have to choose from, comparing the mission statements of these organizations to your own is a great place to start. Charities that align with or complement your own goals as a business are natural partners. Still, while matching big-picture goals is a great start, you also need to make sure your chosen organization aligns with the heart and soul of your business: your employees and customers. FIND HUMAN CONNECTIONS The most powerful charity work your business can support is a cause that stems from the needs and passions of people connected to your work. Maybe a member of your team lives with a disability or a significant number of your customers face social, cultural, or economic challenges. Putting time, money, and effort into supporting a reputable organization that helps the people and communities connected to your business is one of the best ways to show you care. CHECK CREDENTIALS Good intentions only go so far. To really make your charity efforts count and ensure your donations are used appropriately, you need to do some research. Thankfully, organizations like the Better Business Bureau, CharityWatch, and GuideStar. org keep >Page 1 Page 2 Page 3 Page 4
www.cornejocorp.com
Made with FlippingBook - professional solution for displaying marketing and sales documents online