Data Loading...
Vektek Pneumatic Clamping Catalog
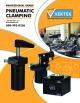
42 Downloads
6.24 MB
Twitter Facebook LinkedIn Copy link
RECOMMEND FLIP-BOOKS
PROFESSIONAL GRADE PNEUMATIC CLAMPING
[email protected] www.vektek.com 800-992-0236
Why use VektorAir ™ ?
Why Use Vektor Air TM ? Since the 1980’s, Vektek has researched, designed, manufactured, direct-sold and serviced the VektorFlo ® line of hydraulic clamping devices. During this time, we have often had requests for pneumatic products. While we have successfully converted many of our hydraulic clamps for air use, we wanted to offer a complete line of pneumatic products, specifically designed to meet the requests we were hearing about. We are now proud to offer you the VektorAir TM line of pneumatic swing clamps, toggles, valves, hardware and plumbing accessories, designed specifically for clamping. We think you will find many uses for these. Durable enough for use in machining and welding operations, they are also a good fit for woodworking, assembly and automation. We’ve created our pneumatic line with the same careful detail to quality that we give our hydraulic clamps. Moreover, we back them with applications staff, our VektorAir TM warranty and our signature service before and after the sale.
Quality Product Quality has always been important to Vektek. This product line is no exception. Some quality features include: PHC TM (Pneumatic Hardcoat), for wrought aluminum surfaces, extends the life of many of our devices. This is a hard anodizing procedure. Internal surfaces are also hard coated and rods are chrome plated for corrosion and maximum abrasion resistance. Magnetic position sensors are available for most cylinders. The channel for the sensor is built into each cylinder already, and all the pistons are magnetized. Simply order the sensor if you want it! It doesn’t add to the envelope of the cylinder since the switch mounts below the clamp surface. LED indicator switches help reduce set-up time. Make connections easily with Vektek’s push-to-connect tubing. It functions with Nylon 11 for inch sizes or Nylon 12 for metric sizes. Fittings are shipped with non-PTFE based thread sealant applied. Standard NPT ports are used. All dynamic seals are made of internally lubricated specially compounded elastomer to promote smooth break away and low operational drag.
WARRANTY Vektek warrants each VektorAir TM product to
the original purchaser unless end user assignment is made at the time of purchase. Each device is warranted against defects in workmanship and materials for a period of six months from the date of delivery. This warranty is limited to the repair or replacement of any part or parts which are found by Vektek to be defective and does not cover ordinary wear and tear, abuse, misapplication, overloading, excessive flow rates, or altered products. This warranty is the only warranty covering VektorAir TM products. There are no other warranties covering VektorAir TM products, either expressed or implied. When question of warranty arises, the user may contact the factory for authorization to return the merchandise. All returned merchandise must be addressed to a Return Authorization number and shipped to the address indicated on the RA.
800-992-0236 © Vektek January 2022
Contents Quick Reference
PLANNING / CONCEPTS Planning Steps 1 - 10.................................................................. A-1 System Examples and Options ..................................................... A-2 SWING CLAMPS Frequently Asked Questions ......................................................... B-1 Standard Features ....................................................................... B-2 Top Flange Threaded Body Specifications....................................... B-3 Bottom Flange Specifications ...................................................... B-4 Position Sensors .......................................................................... B-5 Threaded Body Mounting Hardware............................................... B-6 Arm Specifications ...................................................................... B-7 LINK CLAMPS Frequently Asked Questions ......................................................... C-1 Specifications ............................................................................. C-2 Dimensions ................................................................................ C-3 Lever Dimensions ........................................................................ C-4 SPECIAL USE CLAMPS Air Powered Collet Vise Specifications ........................................... D-1 MISCELLANEOUS PLUMBING Fittings ...................................................................................... E-1 Metric Fittings / Other ................................................................. E-2 Rotary Union, Dual Path .............................................................. E-3 Rotary Union, Quad Path ............................................................. E-4 Tubing / Powered LED Electronic Pressure Switch............................ E-5 VALVES Air Filter Regulator / Air Sensing Control Kit................................... F-1 Confirmation Valve....................................................................... F-2 Check Valve, Manual Valve .......................................................... F-4 Manual Valve, Solenoid Operated Valves ...................................... F-5 Valve, 3 Position, 5 Port .............................................................. F-6 Sub-bases .................................................................................. F-7 Sub-bases .................................................................................. F-8 TOGGLES Features, Frequently Asked Questions ........................................... G-1 Heavy Duty, Vertical .................................................................... G-2 Heavy Duty, Horizontal ............................................................... G-3
A
PLANNING/CONCEPTS
A
SWING CLAMPS
B
B
LINK CLAMPS
C
SPECIAL USE CLAMPS
D
C
MISCELLANEOUS PLUMBING
E
VALVES
F
D
TOGGLES
G
E
SAFETY
F
G
800-992-0236 © Vektek January 2022
Planning/Concepts Planning Steps 1-10
Step 1: First, determine the nature of the operation to be performed, the number of parts to be processed per cycle, and whether operations will be performed on more than one surface of each part. Also, determine the time that should be allowed for part loading, unloading, and clamping. In the initial phases of system planning, include adequate measures and devices to ensure the safety of workers and equipment. For more information, see the safety section on the back inside cover. Step 2: Prepare an outline of the sequence of events that will take place during the manufacturing cycle. This will assist you in determining the types of circuits that you might need, as well as any external control (such as a tie-in with machine controls) that your application may require. Step 3: If you are fixturing for a machine operation, calculate the cutting forces generated in the machining process and note the direction that these forces tend to act on the workpiece. If you are planning a retrofit of a manual clamping system, you may use the torques presently being used. However, it is recommended that cutter forces be calculated as a precaution in such a case to ensure that clamping devices are sized to provide an adequate margin of safety. The operation manuals of many machine tools contain tables that list machining forces or simple formulas for calculating these forces. However, if you can’t find the information, give us a call. We’ll be glad to get you started.
Step 10: Call us for help. Our application engineers do not design fixtures. Their job is to help you use pneumatic clamps successfully, whether you are retrofitting existing fixtures, need an idea (concept) for clamping a new part or want a quick review of your design, we stand ready to help you. Call: 800-992-0236 for everything you need in power clamping... Discover how easy, economical, and efficient power clamping can be with one toll free call. We’ll be glad to answer your questions, provide concepts or advice, and give you a quote.
Step 4:
A-1
When planning for a machine operation fixture(s), plan with positive fixed stops to resist the majority of the cutting forces and to ensure correct location of the workpiece, using the primary part locating features. Step 5: After you have determined the machine cutting forces, it’s easy to calculate the clamping forces required to hold the workpiece on the fixture or machine table. Again, a simple formula is all you need to arrive at an answer for the materials you’ll be using. Give us a call if you need help. Step 6: Determine where clamps should contact the part to hold or support it securely and to avoid interference with operations. If clamps cannot be located so as to avoid interference with manufacturing operations, it will be necessary to use an external control device to move the clamps out of the way as the need arises during the manufacturing sequence. This will require that electrically actuated valving be used to control the offending devices separately. Step 7: Determine the type and number of clamping devices you need based on the total clamping force required and clamping positions you’ve selected; on the size, strength and shape of the part; and on the operation. Step 8: Select valves and other control components to accomplish the sequence of operations you outlined in Step 2 . See the valve section of this catalog for guidance. Step 9: Finally, select the plumbing components required to connect the air supply to the valves and devices. Simply review your system specifications and layout to determine what you need in terms of ratings, sizes, and lengths.
Visit: www.vektek.com to download our most current CAD files.
800-992-0236 © Vektek January 2022
Planning/Concepts System Examples and Options
SYSTEM EXAMPLE Swing Clamps, a Toggle Clamp, Plumbing and a Sensor
Rotary Union (Shown with optional circuit wiring)
Manual Valve
A-2
AIR SOURCE INPUT
SENSOR WIRING SOLENOID CONTROL WIRING
Solenoid Valve
AIR SOURCE INPUT
Clamp shown with Sensor and Wiring
Control Valve Stack Shown with Solenoid Valves (Options: Manual valves -OR- a combination of manual and solenoid valves) Maximum Stack - 5 Valves
MULTIPLE SYSTEM EXAMPLE Swing Clamps, Link Clamps, a Toggle Clamp and Plumbing
SOLENOID CONTROL WIRING
AIR SOURCE INPUT
SOLENOID CONTROL WIRING
800-992-0236 © Vektek January 2022
Swing Clamps Frequently Asked Questions
After clamping, my swing clamps are moving. I cannot detect a leak. Why do I have this movement? Where have you set your minimum operating pressure? When establishing operating pressure for the system, remember that 30 psig is the minimum and must be maintained during cycling. If you set your regulator to 30 psig and then open the valve and the pressure drops to 20 psig during clamping, you need to increase pressure until 30 psig is maintained during the entire clamping cycle. This will prevent cycle problems like the one you describe. We need to regulate the speed of the clamping. How is this best done? If component speed is an issue, always regulate the speed from the opposite side of the piston where the pressure is being applied. In other words, if the return stroke is to be controlled, use the exhaust flow from the extended stroke to regulate the speed. This will give superior control and avoid problems with devices sticking. Is it necessary to use an intensifier? No. You do not need an air intensifier to make your clamps work. Air intensifiers will allow smaller physical size clamps to do more work. For example, referring to the charts on the next page, clamp P1-5110-00 will generate 165 lbs. clamp force at 250 psig, P1-5240-00 will generate 165 lbs. at 60 psig, but is over twice the bore diameter, jumps from 1 7/8” to 3 1/4” in body thread and from about 5 ½” to over 8” in height. If smaller is better, higher-pressure makes swing clamps smaller.
Following are some of the questions we have been asked while developing the VektorAir TM line. Please read them carefully before planning your system. Many common problems can be identified and corrected before you even order a part! Why do I need to know my shop air pressure when planning my system? Your shop air pressure (in psig, pounds per square inch gauge) will help you determine the size clamp necessary to perform the work that you want to accomplish. The pressure should be measured with an accurate gauge at the point nearest the work area and with normal demand on your system. Pressure measured at the compressor is not valid because continuously pressurized gauges are notoriously inaccurate and there is measurable pressure drop over any extended length of pipe, hose or tubing. Demand on your system will result in fluctuations between just a few percent and as much as 50% for an undersized compressor. You will need to know the minimum air pressure supplied continuously to avoid having parts come unclamped or clamps not operating properly. Is it necessary to check our clamping system for air leaks? Yes. Since air used in a pneumatic system is a compressible medium, leakage will dramatically affect clamping loads. Therefore, circuits should be checked with a suitable leak detection solution such as SNOOP ® or equivalent.* * SNOOP ® is a registered trademark of Swagelok ® We shut the air supply down to our clamps once they are in position. Sometimes we notice that they are sticking. Could this be the cause? Yes, you should avoid deadheading clamp circuits. Keep the valve engaged and air flow to the clamps during the entire clamping cycle.
B-1
Can we restrict our swing clamps to rotate less than 90 degrees, or make them rotate further than 90 degrees? Restricting the swing to less than 90 degrees is reasonably simple. We can provide 45 degrees and 60 degrees for a small up-charge. Precise swing angles and those greater than 90 degrees are possible as specials and will be costly. Contact your Vektek representative to discuss special swing clamp needs. Can we modify the standard arm that is included with the swing clamp? Yes, you may modify the standard arm; it is machinable and weldable steel. In order to remove it, please be sure to follow arm removal and re-installation instructions. Remember that larger arms are larger mass and reduced rotational speed is recommended to avoid damage to the rotational cam track. Why would we use a sensor switch with our swing clamps? You may choose to use a position sensor to detect the location of the swing clamp plunger. The sensors can confirm clamp in position, clamp in unclamp position or clamp in neither clamp or unclamp position.
800-992-0236 © Vektek January 2022
Swing Clamps Standard Features
Arms swing 90º. Our capscrew arm design is available. You may modify our arm, or we have provided you with dimensions to make your own. Special wipers and swept-line cylinder tops help keep chips from packing and coolant contaminants from entering the swing clamp. Swing clamp bodies are wrought aluminum alloy with PHC TM (Pneumatic Hardcoat) coating on all external and internal surfaces. This gives the clamps extended life. Plungers are carbon steel with hard chrome plating. The guide bushings are hardened alloy steel. All dynamic seals are internally lubricated and made from a specially compounded elastomer to promote smooth break away and low operational drag. Six bore sizes are available in two mounting styles to best adapt to your application. All models are available in straight pull and left or right swings. Magnetic pistons are standard on all models, allowing you to use position-indicating sensors. Position sensors mount within the clamp’s space envelope so sensor usage doesn’t encroach on the clamp’s mounting envelope. Position sensors have an LED indicator to reduce setup time. All swing clamps have internal orifices to prevent cam damage caused from over accelerating the clamp. VektorAir TM clamps are double acting to reduce mounting envelope and prevent non-return and slow return problems inherent with single acting clamps. To determine whether a straight pull, left or right swing should be specified, imagine D F AA B G E C
Top Flange Threaded Body Swing Clamp
B-2
AG
AF
H
ILSP15002 REV A
Clamp Position Sensor Slot
Bottom Flange Swing Clamp
To
M Clamp Stroke
Str
Unclamp Position Sensor Slot
ILSP15002 REV A
ILSP15201 REV A
Product Clamping Forces
viewing the arm from above during the clamping stroke. Arms moving clockwise are right hand swings, counter-clockwise are left hand swings.
800-992-0236 © Vektek January 2022
ILSP15001 REV D
Swing Clamps Top Flange Threaded Body Specifications
Operating temperature limits are 32-150° F
1/8 NPT RETRACT PORT 1/8 NPT EXTEND PORT RETRACTED SWITCH GROOVE AF A
“N” TOTAL
E
STROKE “M” CLAMPING STROKE
X
G
W
J
AE
B
AA
R
P
B-3
C
Q L°
F
Y
AC
Ø H
D
S
AG EXTENDED SWITCH GROOVE D F C AA B AF
Ø K THRU (4X)
V
AG
POSITION SWITCH GROOVES
AD
Z
AB
T
H
ILSP15000 REV G
V
Swing Direction
T
Top Flange Swing Clamp Model Numbers
4X R
RIGHT HAND LEFT HAND STRAIGHT
P1-5040-00 P1-5046-00 P1-5048-00
P1-5070-00 P1-5076-00 P1-5078-00
P1-5110-00 P1-5116-00 P1-5118-00
P1-5140-00 P1-5146-00 P1-5148-00
P1-5200-00 P1-5206-00 P1-5208-00
P1-5240-00 P1-5246-00 P1-5248-00
N Total Stroke
Clamp Position Sensor Slot Bore
M Clamp Stroke
0.500
0.875
1.125
1.500
2.000
2.500
G
E A 1 1/4 - 16 1 5/8 - 16 1 7/8 - 16 2 5/16 - 16 2 3/4 - 16 3 1/4 - 16 B 4.87 5.48 5.48 8.24 8.24 8.20 C 4.37 4.79 4.79 7.11 7.11 7.07 D 2.75 2.80 2.80 4.28 4.28 4.28 E 0.93 1.17 1.17 1.33 1.33 1.29 F 3.59 3.91 3.91 5.47 5.47 5.47 G 0.31 0.31 0.31 0.31 0.31 0.31 Ø H 0.25 0.50 0.50 0.63 0.63 0.75 J 8-32 x .5 5/16-18 x .5 5/16-18 x .5 3/8-24 x .75 3/8-24 x .75 3/8-24 x .75 Ø K 0.17 0.19 0.19 0.22 0.22 0.28 L° 23 25 25 25 25 25 Unclamp Position Sensor Slot
1/8 NPT Unclamp Port
M RIGHT HAND
0.40 0.40 0.69 0.69 1.44 1.10 0.55 0.94 1.67 0.73
0.47 0.47 0.82 0.82 1.75 1.37 0.69 1.19 2.06 0.87 0.69 1.37 0.88 1.50 5.02 2.19 0.63 0.44
0.47 0.47 0.82 0.82 2.00 1.55 0.78 1.31 2.28 0.97 0.78 1.55 1.00 1.50 5.02 2.19 0.63 0.44
0.75 0.75 1.50 1.50 2.50 1.90 0.95 1.56 2.78 1.22 0.95 1.90 1.25 2.18 7.56 2.99 0.75 0.44
0.75 0.75 1.50 1.50 2.87 2.21 1.10 1.81 3.24 1.43 1.10 2.21 1.44 2.18 7.56 2.99 0.75 0.44
0.75 0.75 1.50 1.50 3.40 2.61 1.30 2.13 3.81 1.68 1.30 2.61 1.70 2.43 7.56 3.31 0.87 0.50
LEFT HAND STRAIGHT
N P Q R S
Top Flange Swing Clamp
• Double Acting (D/A) Cylinders, actuated pneumatically both directions. • Clamps are supplied with a standard arm.
T
V
W 0.55
X Y Z
1.10 0.72 1.13 4.59 1.59 0.38 0.31 8-32 1.56 2.18
AA AB AC AD AE AF AG
1/4 - 20
1/4 - 20
3/8 - 16
3/8 - 16
3/8 - 16
1.76 2.38
1.76 2.38
2.88 3.50
2.88 3.50
2.88 3.50
Effective Piston Area (sq. in.)* - - See * statment far right Extend 0.20 0.60
1.00 0.80
1.77 1.46
3.14 2.83
4.91 4.47
Retract
0.15
0.40
Air Usage (cu. in.) Per complete cycle
0.25
0.80
1.50
5.00
9.00
14.00
800-992-0236 © Vektek January 2022
Swing Clamps Bottom Flange Specifications
1/8 NPT RETRACT PORT AG
G F
“M” CLAMPING STROKE
X
RETRACTED SWITCH GROOVE
W J
AE
“N” TOTAL STROKE
S
AC
R
Ø A
P
Q
B-4
L°
Y
Ø H
POSITION SWITCH GROOVES
1/8 NPT EXTEND PORT
Ø K THRU (4X)
V
AF EXTENDED SWITCH GROOVE
AD
Z
AB
E
T
D
C
ILSP15200 REV F
AA
B
Swing Direction
Bottom Flange Swing Clamp Model Numbers
RIGHT HAND LEFT HAND STRAIGHT
P1-5041-00 P1-5047-00 P1-5049-00
P1-5071-00 P1-5077-00 P1-5079-00
P1-5111-00 P1-5117-00 P1-5119-00
P1-5141-00 P1-5147-00 P1-5149-00
P1-5201-00 P1-5207-00 P1-5209-00
P1-5241-00 P1-5247-00 P1-5249-00
Bore
0.500
0.875
1.125
1.500
2.000
2.500
Ø A
1.19 4.86 4.36 3.67 3.59 0.84 0.56 0.25
1.56 5.48 4.79 3.97 3.91 0.91 0.56 0.50
1.81 5.48 4.79 3.97 3.91 0.91 0.56 0.50
2.25 8.24 7.11 5.61 5.47 0.97 0.62 0.63
2.69 8.24 7.11 5.61 5.47 0.97 0.62 0.63
3.19 8.20 7.07 5.57 5.47 0.97 0.62 0.75
B
C
D E F G
Ø H
J 8-32 x .5 5/16-18 x .5 5/16-18 x .5 3/8-24 x .75 3/8-24 x .75 3/8-24 x .75 Ø K 0.17 0.19 0.19 0.22 0.22 0.28 L° 23 25 25 25 25 25
M RIGHT HAND
0.40 0.40 0.69 0.69 1.44 1.10 0.55 0.94 1.67 0.73
0.47 0.47 0.82 0.82 1.75 1.37 0.69 1.19 2.06 0.87 0.69 1.37 0.88 1.50 5.02 2.19 0.63 0.44
0.47 0.47 0.82 0.82 2.00 1.55 0.78 1.31 2.28 0.97 0.78 1.55 1.00 1.50 5.02 2.19 0.63 0.44
0.75 0.75 1.50 1.50 2.50 1.90 0.95 1.56 2.78 1.22 0.95 1.90 1.25 2.18 7.56 2.99 0.75 0.44
0.75 0.75 1.50 1.50 2.87 2.21 1.10 1.81 3.24 1.43 1.10 2.21 1.44 2.18 7.56 2.99 0.75 0.44
0.75 0.75 1.50 1.50 3.40 2.61 1.30 2.13 3.81 1.68 1.30 2.61 1.70 2.43 7.56 3.31 0.87 0.50
LEFT HAND STRAIGHT
N P Q R S
Bottom Flange Swing Clamp * See graphs on page B-7 for clamp curves and extended arm performance force. It is recommended that the clamp position be set at about 50% of the clamp stroke. These devices should be positioned in no less than 1/2 second. These recommendations apply when using the standard arm. When using the extended or large custom arms, allow 1 second for positioning.
T
V
W 0.55
X Y Z
1.10 0.72 1.13 4.59 1.59 0.38 0.31 8-32 2.12 2.91
AA AB AC AD AE AF AG
1/4 - 20
1/4 - 20
3/8 - 16
3/8 - 16
3/8 - 16
2.37 3.16
2.37 3.16
3.87 4.66
3.87 4.66
3.87 4.66
Effective Piston Area (sq. in.)* - - See * statment far right Extend 0.20 0.60
1.00 0.80
1.77 1.46
3.14 2.83
4.91 4.47
Retract
0.15
0.40
Air Usage (cu. in.) Per complete cycle
0.25
0.80
1.50
5.00
9.00
14.00
800-992-0236 © Vektek January 2022
Swing Clamps Position Sensors
n The use of NPN or PNP is determined by the customer for the device to be connected to the sensor. n 0.188” Sensing Range n Kit Consists of Senor and Cable: - 10 to 30V DC sensor for use in sensing position of swing clamp equipped with magnetic piston.
Position Sensing Kit Model Number and Description P6-2297-00 PNP (Normally Open) P6-2297-01 NPN (Normally Closed)
B-5
- Switch-ON time