Data Loading...
Fruth-CFB Overview

12 Downloads
14.79 MB
Twitter Facebook LinkedIn Copy link
RECOMMEND FLIP-BOOKS
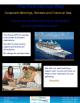
PollinGroup Overview
passengers. PollinGroup will be able to assist in all guests questions, reservations and will send b


Capabilities overview
TPA’s that best fit our client’s objectives On-going assistance in reviewing reports and claim >Page

Melaleuca: An Overview - English
>Page 1 Page 2 Page 3 Page 4 Page 5 Page 6 Page 7 Page 8 Page 9 Page 10 Page 11

UNC Executive Development Overview
UNC Executive Development Overview UNC Executive Development OVERVIEW HOW WE PARTNER with YOU to ACH

Accord - Travelbag Market Overview
Y % + 54 UK £900,000,000 55 40 Overseas 51 £700,000,000 38 Europe 42 £500,000,000 19 Outside Europe

EXPLO | Overview
connections include: NAVIGATING THE SKLLS GAP WHAT TODAY’S STUDENTS NEED TO THRIVE IN 2020 + BEYOND
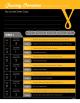
Journey Overview
Social Efforts 1 TOOLS Wish List, Door Price, Training Video # of Journey Based Alerts: FOCUS Meet t

Overview Geographies_2019
withVanna Berlincioni, Virginia De Micco, Alfredo Lombardozzi (referente per Geografie della Psicoan

bswift Overview
bswift Overview Skilled strategy and technology you’d expect. Plus flexibility and agility you might
S E P T EMB E R 2021
T A B L E O F C ON T E N T S
4
T H E S TO R Y O F F R U T H
8 E NG I N E E R I NG E X P E R T I S E & T E C H NO L OG I C A L A D VA N T AG E S
12
MA T E R I A L S
F R U T H MA T E R I A L S
C F B MA T E R I A L S
17
I N D U S T R I E S S E R V E D
19
C L E A N R OOM I N D U S T R Y L E A D E R
3
T H E S TO R Y O F F R U T H
Fruth Custom Packaging: 40 Years of Family, Engineering Innovation and Manufacturing Excellence
Forty years ago, Jim Fruth launched a two-man plastics manufacturing company in Garden Grove, California, just south of Anaheim and north of Huntington Beach. Now Fruth employs 160 people with multiple plants and facilities across Southern California.
Fruth’s modus operandi is steeped in four longstanding, yet simple core values: • Hire top talent • Motivate and inspire excellence • Teach and likewise learn through reciprocated growth • Promote from within when earned
Continuous investment in human capital and commitment to innovation drive company growth year over year.
Fruth’s strategic footprint also includes four acquisitions between 2012 and 2019 when the company expanded its portfolio through the addition of manufacturing facilities and machine and printing shops. And, despite the COVID pandemic, Fruth continues to grow at a pace that far exceeds the competition.
4
100% American Made: The Gold Standard for Specialty Products, Trust and Innovation Whether difficult times or a thriving economy, job creation and retention are consistently coupled with U.S.-made products at Fruth. As a global manufacturer and supplier of custom flexible packaging, Fruth has found its niche in producing specialty products for specialty markets.
From its engineering solutions to custom constructions, formulations and materials, Fruth serves a diversified client base in the automotive, aerospace, medical, pharmaceutical, agricultural, electronic, industrial and luxury goods industries.
More and more customers are seeking alternate packaging options, whether specialty or environmentally certified, and Fruth is uniquely suited to pivot to customer needs because the business is vertically integrated, producing 100% of its products in-house. Family owned and American made, Fruth’s extensive lineup of capabilities leverage the Fruth 360™ process. The vertically integrated manufacturing process allows the company to manage every step of production, from extrusion to conversion to printing and customization, in-house — ensuring the highest quality at every stage of production and saving clients time, budget and peace of mind. And all Fruth products are 100% American made, starting with raw materials sourced domestically. In fact, Fruth was one of the first companies to break down siloed plastics manufacturing that previously required customers to work with multiple companies and vendors to source a finished product — and Fruth does so at a lower price point.
Cleanrooms: Consistency in Manufacturing Excellence
Cleanroom manufacturing is another core business area for Fruth Custom Packaging and Cleanroom Film and Bags, which is currently constructing one of the region’s largest solar deployments to power its newest 28,000 square-foot facility. Cleanrooms are controlled environments custom built to manufacture packaging for medical, pharmaceutical, electronic, aerospace and military devices. These sterile rooms mitigate pollutants such as airborne microbes, aerosol particulates, chemical vapors and dust. They reduce contamination and control other parameters such as temperature, humidity and pressure. At CFB, cleanroom filtration systems are parallel to operating rooms and scientific research facilities. All employees undergo extensive training in contamination control, and gowning is required with masks, gloves, booties and hair coverings to reduce human contaminants like skin cells or hair. But cleanliness is only one part of the cleanroom process. Prevention of packaging additives leaching into products is another core component. Extensive testing is required to ensure no materials used in manufacturing will contaminate the products they are designed to protect. In additon to CFB’s in-house lab testing, including the use of a liquid laser particle counter and other testing methods, CFB undergoes third-party certification to verify the integrity and quality of its cleanroom production. In addition to the Orange County super facility currently under construction, CFB has four other cleanrooms in Southern California. Cleanrooms comprise 55% of the business, driving double-digit growth year over year. The company’s future cleanrooms will empower the company to continue its longstanding vision of custom solutions, top-quality products and innovative engineering expertise.
5
Environmental Awareness: Going Green for a Greater Future
Preparing for the future also includes a close look at Fruth’s environmental initiatives.
Six years ago the company established a green commitment to keep 100% of its industrial scrap out of landfills, the majority of which is recycled back into production. “Our scrap does not go into a landfill, or our groundwater or out into the sunlight where it would sit for 50 to 100 years,” says CEO Jim Fruth. “We’re putting an end to that.” The company has recycled more than 750,000 pounds of scrap annually in the past three years, a testament to Fruth’s green practices which align with core values of building a better future. It also helps drive recruiting and retention efforts. Fruth Custom Packaging has dedicated key stakeholders leading its environmental initiatives, which include installing 440 solar panels at the new cleanroom facility and developing experimental packaging films that will distribute products into Mid-Valley Central California as a pilot program.
6
5 7
E NG I N E E R I NG E X P E R T I S E & T E C H NO L OG I C A L A D VA N T AG E S
8
Fruth + CFB Capabilities & Technological Efficiencies
The companies’ extensive lineup of capabilities leverage the Fruth 360 ™ process. This vertically integrated manufacturing process allows the FCP and CF B to manage every step of production, from extrusion to conversion to customization, in-house — ensuring the highest quality at every stage of production and saving clients’ time, budget and peace of mind.
Fruth is the West Coast’s premier vertically integrated plastics manufacturing facility.
C L E A N R OOM With more than 35 years’ experience, our engineering expertise, customization capabilities and rapid go-to-market resources makes CFB the cleanroom packaging industry’s go-to partner.
From packaging for cutting-edge microchips to life-saving medical equipment and everything in between – CFB has you covered.
Our state-of-the art cleanrooms not only meet the highest level of compliance (ISO 9001:2015 compliant and IEST Standards STD, bags certified up to Level 50) but are vertically integrated, equipping CFB with the ability to meet the unique demands of every customer while creating superior quality packaging within the microelectronic, aerospace, semiconductor, silicon, food and medical markets.
9
CON V E R S I ON Our state-of-the-art-technology combined with decades of expertise give us the unique ability to engineer, manufacture and convert a wide variety of high-quality LDPE products for our customers. We offer LDPE products in 1-10 ml. thickness and an extensive range of colors. Our extruded, blown- film and heat-sealable materials can be converted into custom small or large bags. They can also be ordered as standard tubing or sheeting rolls from 1/2”″ to 82”″ wide.
C U S TOM I Z A T I ON A commitment to customization allows us to deliver packaging our competitors can’t. Our team is committed to providing an extensive range of high-quality flexible packaging products at the most competitive price. We will meet your unique business needs from small to large production runs with quick turn-around times. From engineering to quoting to manufacturing to arranging low-cost shipping, and all the steps in between, we treat our customers with the care and attention they deserve while supplying quality-assured manufactured goods at the most affordable prices.
We’re always up for the challenge — going where others fail to go.
E X T R U S I ON Fruth specializes in custom single wound sheeting, centerfold sheeting and tubing plastic extrusion. We produce film from 0.5” to 82” wide and can run 1.5 ml. (.0015) to 15 ml. (.015). Roll length is determined by width, thickness and weight. We extrude LDPE, LLDPE, medium to high density polyethylene, as well as polypropylene. Additionally, our diverse selection of additives allows us to produce a wide variety of polyethylene with specific protective barriers including:
• Ethylene Vinyl Acetate - EVA • Ultra Violet Blocking - UVB • Volatile Corrosion Inhibitors - VCI • Anti-Static • Black Conductive • Green Nuclear • Mono-extruded nylon film and virgin/barefoot film for cleanroom use
10
P R I N T I NG Our in-house printing capabilities have been a cornerstone of our product line for years. We recently invested in new equipment and employee training to develop our new printing department. With the ability to print up to six colors on two sides of film (max length 22”), your branding and artwork will look incredible on our poly bags. We use custom flexographic plates and accurate color matching to ensure the highest quality printed bags and film. Printed film can be shipped on rolls or converted into bags with zippers or lip and tape closures, and can include features such as bottom gussets, side gussets, perforations, hole punches, and two pocket zipper or multi-pocket configurations. Printed film can range in thickness from 2 to 6 ml. We use our flexographic printing presses to provide customers clean and accurate printing on a range of materials, from industrial poly to high-performance specialty films.
R E P R O C E S S I NG Our reprocessing technology allows us to recycle 100% of our high-quality resins and 50-75% on many of our commercial jobs, resulting in a 60% average reduction in materials costs.
Products that utilize high-quality resins (high-quantity of LDPE) often see net margins exceeding 40%.
In conjunction with our reprocessing capabilities, we have the capacity to sell off excess production at high-market prices — in many cases 75-80% of current virgin resin supply. This creates an additional profit center driven by Fruth’s state-of-the-art technology.
S T E M H A R DWA R E In the continual pursuit of profitability Fruth has installed STEM hardware to reduce energy costs. This hardware (30 kw at Fruth, 5kw at CFB) allows amp-sharing utilizing inexpensive nighttime charging energy and discharges it at peak- time during the high-rate daily times. Fruth was the pilot manufacturing plant installation in 2016, and it has resulted in significant energy savings in our electrical bids.
TOO L I NG Our in-house tooling machine shop provides limitless engineering solutions to the custom demands of very intricate packaging products. Not only do these tooling improvements bring new project capabilities, this engineering capability ensures the constant application of the lean manufacturing 6S methodology across the manufacturing ecosystem.
11
MA T E R I A L S
12
F R U T H MA T E R I A L S
714.993.9955
sales @ fruth.com
701 S. Richfield Rd. Placentia, CA 92870
Fruth 360 ™ Process Fruth has a vertically integrated manufacturing process that allows us to manage every step of production, from extrusion to con- version to customization. This allows us to ensure the highest quality at every stage of production and saves clients’ time, budget and peace of mind. We are the West Coast's premier vertically integrated plastic manufacturing facility. Material Offerings
701 S. Richfield Rd. Placentia, CA 92870 Fruth Custom Packaging is an innovative leader in cleanroom packaging technology, providing the ultimate cleanroom products while meeting the most stringent industry requirements! Cleanroom Level 100 Fruth Custom Packaging is an innovative leader in cleanroom packaging technology, providing the ultimate cleanroom products while meeting the most stringent industry requirements! Cleanroom Level 100 C LEVEL 100
Poly LDPE, LLDPE, MDPE & HDPE Industrial, FDA, or Barefoot Autoclavable Polypropylene UV Light Inhibitors (UVI) Volatile Corrosion Inhibitors (VCI) Ethylene Vinyl Acetate (EVA) Extremely Low Outgassing (FELO) Custom Colors, Tinted & Opaque Thicknesses of 1.5 ml through 10ml Nylon Mono-Extruded (Cle r / A/S) Co-Extruded Biaxially Oriented Material Offerings Industrial, FDA, or Barefoot Autoclavable Polypropylene UV Light Inhibitors (UVI) Volatile Corrosion Inhibitors (VCI) Ethylene Vinyl Acetate (EVA) Poly LDPE, LLDPE, MDPE & HDPE Extremely Low Outgassing (FELO) Custom Colors, Tinted & Opaque Thicknesses of 1.5 ml through 10ml Nylon
714.993.9955 Protective Packaging Foam (White / Pink) - 3/32” and less Bubble (Clear and Anti Stat - 1/8” and less) Bubble (Cancel – Clear and Anti Stat) Foil Bubble (Thermal Protection) Multi-Layer Pouches Biohazard Protective Packaging Foam (White / Pink) - 3/32” and less Bubble (Clear and Anti Stat - 1/8” and less) Bubble (Cancel – Clear and Anti Stat) Foil Bubble (Thermal Protection) Multi-Layer Pouches Biohazard Pink & Clear Anti Static Poly Black Conductive Static Shielding EMI Static Shielding Barrier & Anti-Static MVTR and Oxygen Barrier Mil Spec Vacuum Pack Pink & Clear Anti Static Poly Black Conductive Static Shielding EMI Static Shielding Barrier & A ti-Static MVTR and Oxygen Barrier Mil Spec Vacuum Pack
sales @ fruth.com
C
LEVEL 100
Mono-Extruded (Clear / A/S) Co-Extruded Biaxially Oriented
714.993.9955
sales @ fruth.com
701 S. Richfield Rd. Placentia, CA 92870
Custom Construction Options
Bags Flat Side and Bottom Gusset Zipper Lip and Tape On W ickets Bags Flat Side and Bottom Gusset Zipper Lip and Tape On W ickets Multi Pockets and Compartments Vista (1 side clear / 1 side colored) Square Bottom Covers and Liners Roll Stock Tubing Gusseted Tubing Single Wound Sheeting Centerfold Sheeting J-Fold Sheeting Perforated on Bags on Rolls Multi Pockets and Compartments Vista (1 side clear / 1 side colored) Square Bottom Covers and Liners Roll Stock Tubing Gusseted Tubing Single Wound Sheeting Centerfold Sheeting J-Fold Sheeting Perforated on Bags on Rolls
714.993.9955
sales @ fruth.com
701 S. Richfield Rd. Placentia, CA 92870
Custom Construction Options
Custom Engineering
Custom Engineering With 30 years of experience making bags and developing custom solutions to build your products, Fruth Custom Packaging is uniquely positioned to provide custom machinery solutions to make your imagin a tive p ackaging designs a reality. Our new corporate addition, TecHouse Machining, lends its expertise in machine design and construction to build the perfect packagin g solution for your needs. With 30 years of experience making bags and developing custom solutions to build your products, Fruth Custom Packaging is uniquely positioned to provide custom machinery solutions to make your imagin a tive p ackaging designs a reality. Our new corporate addition, TecHouse Machining, lends its expertise in machine design and construction to build the perfect packagin g solution for your needs.
13
F I L M S P E C I F I C A T I ON S
Aclar Extremely low OTR and MVTR transparent barrier films. Used primarily for pharmaceuticals. Maintains properties at cryogenic temperatures. Anti-Static Protects from static electricity, using a static dissipative polyethylene surface. Bio-Friendly Using a special biodegradable additive, this film will break down faster than regular polyethylene in the presence of moisture and air. Black Conductive Non-sparking carbon loaded polyethylene, meeting specifications detailed in MIL-DTL-82647. Used for ammunitions, explosives, etc. CP STAT 100M Static Shielding film that complies with specifications detailed in MIL-PRF-81705 Type III, Class 2. EMI Static Shielding Foil structure that complies with MIL-PRF-81705 Type I, Class 1. Protects from static electricity as well as magnetic fields. Film Foil Poly Foil and polyethylene structure, compliant with specifications detailed in MIL-PRF-131K Class 1. Will hold a long-term vacuum. Excellent moisture vapor protection. Flame Retardant Self-extinguishing film, compliant with the NFPA 701 Small Scale test. Mostly used for aerospace items in long-term storage. Green Nuclear Polyethylene meeting stringent specifications detailed in the MIL-DTL-24466 DOD specification. Mostly used at military bases (primarily naval).
Kraft Foil Paper and foil structure, meeting all specifications required in MIL-PRF-131K Class 2. Frequently used when protection from grease is required. Low Density Polyethylene General purpose packaging film. Available with countless custom performance additives, colors, print options, conversion options. Endless possibilities.
Medium/High Density High strength polyethylene. Won’t leave residue on glass items.
Nylon Non-sloughing mono-extruded nylon. Good oxygen barrier. Commonly used in cleanrooms and aerospace applications. Polypropylene Autoclavable, medical hazardous waste disposal, use in hospitals for waste requiring high temperature sterilization. Poly Aclar Very stable transparent film, that won’t slough off contaminants over time. Good moisture vapor protection. Complies with specifications detailed in MIL-PRF-22191, Type II, Class 2.
Poly Mylar Transparent structure. Good moisture vapor protection.
Static Shielding Transparent metallized structure. Used to protect from static electricity. Used primarily with ESD grounding equipment. Tyvek Foil Foil structure with a Tyvek layer. Complies with all specifications detailed in MIL-PRF-131K Class 1. Used in applications requir- ing light blocking or ethylene oxide sterilization.
VCI (Volatile Corrosive Inhibitor) Used to protect ferrous metals from rust or corrosion.
14
15
C F B MA T E R I A L S
CFB Products: All Poly products extruded, converted and packaged in an ISO-certified cleanroom. At Cleanroom Film and Bags, we pride ourselves on our high level of quality through the use of the latest technologies in cleanroom extrusion and conversion processes.
Materials Polyethylene - LDPE, MDPE, & HDPE Cleantuff Ultra Low Outgassing (ULO ® ) Nylon Poly/Nylon ESD Packaging Anti-Static Static-Shielding Barrier Film
Cleaning and Testing Aerospace and Military Boeing and Honeywell Approved Lawrence Livermore National Laboratory Approved ISO 9001:2008 Compliant Cleanliness Testing Pressure Testing NVR Testing Creep Testing Burst Testing Film Cleaning Service We can clean many films to NASA JPG CC 5322.1 or IEST-STD CC 1246E Standards.
Packaging Types Bottom Seal Zipper Bags Square Bottom Covers Bags on a Roll Pre-Opened on a Roll Pouch Seal Tubing & Sheeting Packaging Size Range 1” to 80” Width 1” to any Length Gauge to 14 ml Gusseted to 12 ml
Cleanliness All polyethylene packaging is extruded, converted and vacuum sealed in a specially designed cleanroom facility, using proprietary resin formulations. This results in films that require no additives and exhibit unmatched cleanliness levels. Quality Assurance Our films are tested on-site using a Liquid Laser Particle Counter. This practice ensures the cleanest film possible. Bags undergo pressure and leak testing to verify a strong seal and a perfect bag. Full chemical analysis of our materials is available upon request.
16
I N D U S T R I E S + C L I E N T S S E R V E D
17
14
I N D U S T R I E S WE S E R V E
A U TOMOT I V E • Oil Filter Disposal • VCI to protect engine parts from rust and corrosion • Document Holders
C ON S UM E R GOO D S • Fishing Equipment • Furniture Covers • Golf Bags • Ice Bags • Sports Equipment • Pillow/Mattress Covers • Specialty Food Items • Spice Mixes
A E R O S PA C E • Barrier Packaging • ESD Packaging • Large Part Transit Covers • Cleanroom • Flame Retardant
I N D U S T R I A L • Extra Strength Additives • Extra Strong Foils (puncture resistant) • Nuts, Bolts, Screws • Tools • Corrosion / Rust Protection • Multiuse Column Bags • Recycling M I L I T A R Y • Weapons Storage • Green Nuclear (used by naval institutions)
AG R I C U L T U R A L • Grow Bags (to replace hard plastic containers) • Covers for Crops or Greenhouse structures • Seed Bags • Fertilizer Bags M E D I C A L / B I O - P H A R MA C E U T I C A L • Cleanroom • Medical Device • Catheter Wires (thin tubing) • Autoclave for Sterilization • Compatible for Irradiation Sterilization • Cleanroom Packaging • Certified Class/Level 100/ISO Class 5
• Black Conductive • Flame Retardant • Mil Spec Packaging
P R OT E C T I V E PA C K AG I NG • Bubble Bags • Foam Bags • Multi-Layer Cushioned Bags S E M I - C ON D U C TO R • Cleanroom Packaging • Non-Mar • Silicone Wafers • Quartz • Glass C U S TOM • Design • Zipper • Pockets • Print • Perf’s • Wicket • Anything you can think of...
E L E C T R ON I C S • Static Control Packaging
– Static Shielding – Anti-Static Poly – Black Conductive – Cushioned Static Shielding Bags
E N V I R ONM E N T • Light Proof (UVI) • Barrier Protection from all Environmental Elements
18
C L E A N R OOM I N D U S T R Y L E A D E R
19
C L E A N R OOM PA C K AG I NG : MA N U F A C T U R I NG P R O C E S S A N D D E T A I L S
Cleanroom Levels
L E V E L 10 0 Articles requiring cleanliness Level 100 are extruded and converted with our FCR-1000 polyethylene or FCN-6000 cleanroom nylon film. Regular cleaning, proper handling and gowning procedures, and an ISO Class 5 cleanroom with low airborne particulate ensure the surface particulate of our bags meet and exceed requirements defined in the IEST- STD-CC-1246E Level 100 declaration. The items are then double bagged, vacuum sealed and shipped in appropriate, cleanroom compatible boxes with cleanroom compatible labels. L E V E L 10 , 0 0 0 Articles requiring cleanliness Level 10,000, are extruded and converted with our FCR-1000 polyethylene or FCN-6000 cleanroom nylon film and are manufactured to meet Level 10,000 specifications. Certain items, such as our square bottom covers, are cleaned by hand and wiped down after construction to remove oils, dirt and particulate that may have collected during processes that require excessive handling.
20
Cleanroom Protocols
Documents used to establish cleanroom protocol and acceptable allowable particle counts are:
• ISO 14644-1 (formerly MIL STD 1246C): Details the specific cleanroom environment requirements for airborne particulate and personnel protocol, including the details for our cleanroom to meet the Class 5 designation. • IEST-STD-CC1246E (formerly Federal Standard 209E): Details the surface particle allowance, including Level 100 and Level 10,000. • NASA JPR 5322.1 Rev F: Details surface particulate as is allowed by NASA and Federal requirements. T E S T I NG Our cleanrooms are tested by an outside auditing agency. Liquid laser particle counting, Elmendorf tear, and tensile strength and elongation is performed onsite in our testing labs. NVR, F.T.I.R., SEMS, Chromatography and other related tests are conducted by an outside Lab. Test results for individual production lots are available upon request, at the customers cost.
MA T E R I A L S FCR-1000 Series Polyethylene Film
Orders received at Fruth Custom Packaging that call for a Level 10,000 or Level 100 specification are made with a proprietary blend of resin referred to as FCR-1000 and its subsequent variations. This resin compound consists of a virgin polyethylene resin base that is free of all additives including slip and anti-block. Elimination of these additives produces film that has a non-marring, non-scratching surface, perfect for the packaging of critical soft metal and plastic parts typically used in a cleanroom environment.
Our FCR-1000 cleanroom polyethylene is extruded in our cleanroom that meets or exceeds all requirements called for in ISO 14644, Class 5 (formerly Federal Standard 209E). Our blown film extrusion process uses clean, filtered, nitrogen purged air to avoid introducing airborne particulate to the interior surface of the film. Extruded film is wound on clean, plastic cores to avoid contamination with particulate from traditional spiral paper cores. Tubing rolls are individually wrapped and boxed. Every effort is made to handle the material with extreme care, as scraped or abraded film can generate particulate off of the surface of the material.
All raw cleanroom materials are purchased from our approved suppliers, in lot numbered gaylords for lot traceability and supplier accountability.
FCN-6000 Series Nylon Film In the processes for manufacturing our FCN-6000 Series Nylon bags, ultimate measures are taken to remove impurities from the film and to control environmental factors such as air cleanliness and atmospheric moisture vapor content. Every effort is made to ensure both the inside and outside of the film is clean, and our machinery is designed to eliminate any particulate or contaminants during the manufacturing process. Our FCN-6000 Series bags meet or exceed all requirements called for under IEST 1246E Level 100 specifications. This film is used in place of polyethylene in applications when a lower OTR and MVTR is necessary. This will protect from gas, aroma, chemicals, and moisture, and provides extra exterior strength and puncture resistance.
21