Data Loading...
Quest Safety/Lilly Overview

8 Downloads
3.85 MB
Twitter Facebook LinkedIn Copy link
RECOMMEND FLIP-BOOKS
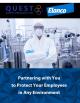
Quest Overview-Pharma-Elanco
Supply Chain to Fit a Company’s Specific Needs Documented Supply Chain for Aseptic Products Q Safe S


Quest Safety Products Overview: Life Science Industry
Supply Chain to Fit a Company’s Specific Needs Documented Supply Chain for Aseptic Products As a fur

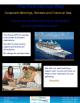
PollinGroup Overview
passengers. PollinGroup will be able to assist in all guests questions, reservations and will send b

Quest Controlled Environment Catalog
cs Facemasks Goggles Item #: Size MD Item #: Size Item #: BDHD-L Size Item #: Size IC666BWHMD01000C


Capabilities overview
TPA’s that best fit our client’s objectives On-going assistance in reviewing reports and claim >Page

Melaleuca: An Overview - English
>Page 1 Page 2 Page 3 Page 4 Page 5 Page 6 Page 7 Page 8 Page 9 Page 10 Page 11

UNC Executive Development Overview
UNC Executive Development Overview UNC Executive Development OVERVIEW HOW WE PARTNER with YOU to ACH
Partnering with You to Protect Your Employees in Any Environment
Quest Overview
Customer Prioritization
Our Focus Partnering with Companies to Help Protect Their Workers in Any Environment Our Focus is on Your People Your Products Your Facility
Our Mission To see that Every Worker Makes it Home Safely at the End of Each Day
• Safety • Communication • Transparency • Delivery • Keeping Promises • Cost Controls • Operational Efficiency
Distributor & Manufacturer We are a distributor of lab, safety, and packaging supplies as well as amanufacturer of cleanroomgarments. We moved into manufacturing disposable garments in 2002 when Lilly needed a stronger supply chain partner for garments. That effort satisfied Lilly’s government mandates and resulted in a $250,000 per year cost reduction in one business unit for Lilly. Proven Experience Serving Pharmaceutical Companies Quest Safety currently works with 11 of the top pharmaceutical companies providing technical expertise, competitive pricing, and supply chain consistency. The pharmaceutical market is the fastest growing industry for Quest and continues to be an integral part of our business. Trusted Partner Quest Safety Has 20+ Years Working with Lilly! You have consistently been serviced by the same two Account Managers that entire time. We continuously work with your interest in mind – proactively providing the best safety solution available, plus cost savings, increased productivity, and an ease of doing business. Our business model puts you first. We moved to downtown Indy and applied for HUBZone certification at the request of Lilly to help Lilly satisfy federal HUBZone spending requirements. Solution Provider Quest provides more than products and equipment; we provide the solutions that solve problems and keep workers safe. Some of our solutions involve: • Cost Saving • Inventory Alignment Strategies • Safety Audits • Customizations • Training • VMI Our solutions for Lilly have totaled over $2.5 million over the past 18 years. As a partner to pharma companies, Quest is tested daily on competitive pricing, product quality, on-time delivery, and supply chain consistency. 2020 challenged many suppliers’ procurement practices. Quest was able to navigate these uncharted waters providing critical products to Lilly with 0 stock-outs or near- misses. As a result, the IPM business unit was able to supply critical material globally to aid other sites stock out concerns.
Our Associations and Certifications
Make Us a Stronger Partner for You
HUBZone & MBE Certified (HUBZone: Historically Underutilized Business Zone MBE: Minority Business Enterprise)
Buying Power as a Member of AD AD is a member-owned organization, bringing independent distributors and best-in-class supplier partners together to achieve annual sales of $46 billion across nine industries and three countries. AD’s buying power gives Quest the ability to purchase items at discounted prices only afforded to giant companies in the past. The power of AD gives Quest strong relationships and bargaining power with the top safety product manufacturers like 3M, Honeywell, Kimberly-Clark, Radians, Revco, DuPont, Ansell, Lakeland, and more. Through these relationships, our customers get better pricing and interaction with manufacturers. Member of Diversity Alliance for Science Quest has actively participated in strengthening supplier diversity within the life science industries since 2005. Our interaction within the Pharmaceutical Industry keeps us abreast of changes in the industry. Quest became a NMSDC Corporate Plus member in 2022. Corporate Plus® members have demonstrated their capacity to execute national contracts for major corporations. NMSDC national corporate members nominate MBEs for this designation, which elevates their profile among national corporate members and facilitates the MBEs broader participation throughout the NMSDC network. Quest can help you manage and satisfy your federal contract spend requirements. Audited by a PSCI (Pharmaceutical Supply Chain Initiative) Member Company Quest was audited by AbbVie Pharmaceuticals in 2019. Our new facility will be audited by the end of the year. Rest assured that our business practices and facilities match the needs of the Pharmaceutical Industry.
Providing aWide Range Pharmaceutical
Protective Apparel
CE Manufacturing
(Clean, Sterile, Non-Sterile) • Shoe Covers • Boot Covers • Coveralls
• Absorbents • Laboratory Dispensing Containers • Laboratory HPLC Safety Disposal Cans and Containers • Laboratory Carboys and Solvent Waste Systems and Accessories • Material Handling Equipment (Specializing in Vacuum Lift Equipment)
• Frocks • Gowns • Gloves • Sleeves • Facemasks
• Hoods • PAPRs
of Supplies for Companies
Laboratory and Critical Environments
Industrial/MRO
• PPE (Personal Protective Equipment) • Gas Monitoring Equipment & Calibrated Gas • Ergonomic Equipment & Matting • Arc Flash and FR Protection
• Lab Wipers (Pre-saturated wipes to general cleaning and bench protectors) • Sample Bottles/Jars (Qorpak, Silgan) • Caps, Closures, and Lids • Vials and Lab Tubes • Plastic Bags for various lab applications • Cleanroom Equipment • Restricted Access Barrier Gloves (RABS)
• Signage and Labels • Traffic Equipment • Absorbents & Spill Prevention
• Safety Cabinets/Storage • Chemicals & Disinfectants
• Sampling Bags • Biohazard Bags
Material Handling • Fiber Drums
• Aluminum and Plastic Pallets • Slip Sheets and Trailer Liners • Corrugated Pallets, Boxes, Liners
Why Life Science Manufacturers Choose Quest
Partnership Focus Compliance to Quality Products.
Will only deliver items from Approved Suppler List (ASL) - NO UNAPPROVED SUBS….EVER Cost Savings Initiatives Competitive Pricing Transparency and Reporting Flexibility in Procurement
Overhead Reduction Product Standardization Lowers Costs
International Sourcing
Inventory Alignment Strategies
Inventory Management
Operational Efficiency
• Inventory Accuracy Rate of 99.8% • Order Accuracy Rate of 99.4%
Strong Foundation Experience : Over 25 Years of Experience Creating Safety Solutions
Technical Training : Safety Equipment Expert (SEE) Certification through AD SafetyNetwork.me, Qualified Safety Sales Professional Certification, Member of the local ASSE chapter
Reliability : Consistent Supply Chain, Dedicated Account Team
Responsiveness : Strong Customer Support
Connected : A Member of AD SafetyNetwork.me, the Largest Buying Group in the US with Over $1 Billion in Buying Power and Connections throughout the Safety Industry.
Quest gets approval from Safety, IH, and Procurement departments with our Pharma customers before any products are sold/delivered to their facilities.
Sourcing/Supply Chain Experience Resource and Advocate for Providing Product Needs and Solutions
Building Specifications and Processes to Increase Efficiency
Designing Products/Supply Chain to Fit a Company’s Specific Needs
Documented Supply Chain for Aseptic Products
As a further commitment to our customers and the SBA HUBZone program, Quest has made a $5.5 million investment of a new 60,000 sq. ft. facility. This is an additional 33,000 sq. ft. from our previous facility.
Investing in America’s Future to Support Our Customers’ Growth
Increased warehouse capacity allows us to expand our in-stock product offering.
We have also added an Isolated Storage Room for critical pharmaceutical items.
We have started the FDA Registration process and plan to have the PSCI Audit completed by end of year. This video shows how our new facility will enable us to better serve Life Science customers. You can also find the video on Quest Safety Products' YouTube home page.
Recognition
2018 Top Diverse Supplier Award from AstraZeneca
During the award presentation, Diana Vass, Sr. Buyer at AstraZeneca, told the summit attendees that the awards given at the AstraZeneca Supplier Summit highlight suppliers that exemplify the following qualities: • Good Business Partner (Collaborative in Nature, Offering Transparent Business Practices, Responsiveness) • Striving for Continuous Improvement • Focusing on Innovation • Promoting Economic Development • Donates to Their Local Communities • Follows a Similar Mission Statement
2018 HUBZone Champion Award from The HUBZone Contractors National Council The 2018 HUBZone Champion award is given to companies that focus on promoting the values and spirit of the HUBZone Program and are involved in community outreach and support.
“The HUBZone Contractors National Council was proud to present Sam Yadav of Quest Safety Products the HUBZone Champion Award at the 2018 National HUBZone Conference. Reading how Mr. Yadav and the Quest team banded together to secure over 210,000 dollars in supplies and gear for the first respondents during Hurricane Harvey is beyond amazing.” Michelle Burnett, Acting Executive Director of The HUBZone Contractors National Council
Nominated for Supplier of the Year 2021 – Diversity Alliance for Science
Key Projects with Lilly
2000-2001
1999
Eli Lilly asked Quest to team with Flour Daniels Construction on a major project at Lilly Technology Center (LTC) requiring tight schedules & ZERO incident rating. To build a constant supply chain, Quest developed a disposable garment design to fit the end user needs, secured the raw materials, contract manufacturing group, and managed the quality control/supply chain of the garment for the project. Quest was the only supplier on the $1 Billion project that did not miss a deadline.
Quest gained our first set of Safety Customers - Utilities and Construction companies working on Eli Lilly’s campus.
2002
• Eli Lilly asked us to use the same expertise shown on the Lilly LTC project to help reduce disposable garment cost, resulted in a $250,000 per year cost reduction in one business unit. • Awarded Eli Lilly Global Supplier of the year.
2004
• Awarded Eli Lilly MRO Safety Contract. • Quest Began Vendor Managed Inventory at Lilly Technology Center and 2 other customer locations in Indianapolis. • Lilly Purchase Order management, working with end user and procurement Quest gives notice as the PO owner is getting to the end of the PO life.
2016
2017-2019
Quest participated in the first Lilly Mentorship Program under Andrew Dahlem, Chief Operating Office of Lilly Research Labs (Retired).
Implemented Fiber Drum Conversion providing Lilly with over $57,000 in cost savings.
Historical View of Business Units Served by Quest
• LTC North
• Fermentation • Compliance Labs • Clinical Trials Operations
• LTC South • API • BHI • IPM • IDAP
• Chem Dispensing • Indy Stores • Plainfield: NALO • Lilly NJ: Branchburg NJ
• Lilly NJ:
Branchburg NJ
• Indy Stores • Plainfield: NALO
The Benefits of Quest Safety’s Vendor Managed Inventory (VMI) Program We focus on you having your products stocked when you need them so your employees can focus on your bottom line.
Increased Customer Care Regular access to Quest’s VMI and customer service team. Product availability boosts the quality of customer service. Reduced Inventory Overstocks & Stock Shortages Not having the right products in stock can impact quality of work. Quest’s VMI can reduce overstocks and stock shortages that cause uncertainty. Improved Operational Efficiencies Quest’s VMI program decreases a Lilly employee’s time to manage product inventory as well as insures consistent supply of the right product at the right time. Onsite Technical Expertise Quest’s experience in VMI allows us to bring our customers better reporting and reduces administrative work so our customers can focus more strategically on areas of their business. Financial Transparency Site-specific reporting and spend usage allows our customers to make better- informed business decisions and eliminate wastage, non-value adding factors, and other costs associated with inventory errors.
Finding Cost Savings through Standardization
Step 1: Understand We first gain an understanding of your business and application needs. It is important to understand what products are being used and why. We work with the end user to understand possible workplace hazards and the features and benefits of the product being used. Step 2: Analyze and Identify We analyze that >Page 1 Page 2 Page 3 Page 4 Page 5 Page 6 Page 7 Page 8 Page 9 Page 10 Page 11 Page 12 Page 13 Page 14 Page 15 Page 16 Page 17 Page 18 Page 19 Page 20
Made with FlippingBook Ebook Creator